Feature
The F1 ‘super-weapon’? How the development battle between the Formula 1 factories has ignited the 2024 season
Share
The first half of an explosive season is completed – but it’s the battles in the factories as much as the ones on track that have ignited 2024.
It seems a long time ago now, but back in March and April, F1 2024 looked like a rather one-sided affair. Max Verstappen won four out of the first five races, and likely only a stuck brake calliper in Albert Park prevented a clean sweep. Red Bull Racing and the RB20 had it in the bag. Until they didn’t. With the first upgrade cycle, everything changed.
It’s not a coincidence that McLaren delivered their first upgrade in Miami and won that race – probably with the fastest car. Ferrari fitted theirs at Imola, and a week later were top of the pile in Monaco. Mercedes took a little longer to get out of the blocks but arguably made the bigger leaps with their upgrade package, winning three of the final four Grands Prix before the break.
Aston Martin, on the other hand, fell down the order after an upgrade failed to ignite. Red Bull give every appearance of struggling to squeeze more out of the RB20, and thus have slipped from a position of dominance to merely being the first among equals – and with the Belgian Grand Prix demonstrating how incredibly tight the front of the grid is at the moment, there’s potential for the climax of the 2024 season to be determined by who can deliver more to the car after the break.
Can Red Bull squeeze more out of the RB20 when the season resumes after the summer break?
Cars and the cap
There’s often a misconception that the success of a team's upgrades is about the speed and prowess of a design department. It isn’t. Or rather, it isn’t just about design: increasingly, it’s about how quickly a team can physically make the parts.
Get your upgrade out a race ahead of the competition, and you gain not only that immediate pace advantage but also the extra benefit of it being dialled in and studied before subsequent races. Consistently get your upgrades out early, or produce them more cost-effectively with less waste, and perhaps you can squeeze one more in across the season. It’s a performance super-weapon.
READ MORE: Hamilton predicts ‘one hell of a second half’ to 2024 amid multi-team scrap for wins
There is an understanding that an F1 car changes specification from race to race, sometimes even day to day. These are, after all, prototypes, permanently being nipped and tucked. The major upgrade, however, is an all-together grander undertaking.
Planned months in advance, with two, perhaps three scheduled across the season and frequently with parts not interchangeable with previous versions, it can be a game-changer – but in the era of the cost cap, changing the game is something to be considered very carefully.
Particularly for the larger squads, there’s a new form of discipline imposed by the cap, with budget rather than time being the decisive factor. Whereas previously teams might outsource component build to specialist suppliers, the cost associated with doing so is high. And while teams won’t entirely stop sending work out, there’s a greater focus now on keeping it in-house wherever possible. Having a lean, efficient factory has become as crucial to delivering points as a slick pit stop crew or clever strategy.
Significant upgrades – like the new front wing Mercedes debuted on Russell's car in Monaco – can be a game-changer for a team
Running lean, reducing waste
The first example of quite how tight teams run things came very early in the season, when Williams stood down Logan Sargeant in Australia. Having damaged one chassis in practice, they didn’t have a spare available, and the young American was the driver to pay the price.
The team had prioritised performance updates over spares, and were pilloried for their choices – though they were by no means alone in that decision, and even teams with chassis #3 ready before the season start were sailing close to the wind in other areas.
TECH WEEKLY: The 3 most significant technical developments of the 2024 season so far
McLaren are coy about when and where they’ve been racing with the cupboard bare this year – though they’re happy to reveal that it has happened, and that it's simply how it has to be.
“We occasionally have to be okay with being uncomfortable,” concedes Chief Operating Officer Piers Thynne. “We wouldn’t put the car out with no spares – but there are no World Championship points for parts sitting in the truck. Effectively, it’s a risk-trade. If you don’t take that risk, you’re just creating waste – which is not the way to win.”
Thynne has been heavily involved in leading McLaren’s production operation, having previously been Production Director and then Operations Director. He’s one of the people responsible for deciding what parts and how many to manufacture, and when to manufacture it. With somewhere between 10,000-12,000 parts in manufacture at any given time, it can be quite the balancing act.
McLaren ran a significant upgrade at the Miami Grand Prix – but have otherwise not brought many updates during the first half of the campaign
“Over the last five years, we’ve gone leaner, leaner, leaner and we’re coming up to a hard stop. We’d never just make two of something – but we are making trades. We want it all – but there’s a cost cap. If we’re doing one thing, what are we not going to do?
“It's all performance-led. We might trade circuit-specific items in favour of things that would give us opportunity to score points over a wider number of tracks. It’s all about getting that trade and risk right. We don’t get it right all the time – but we’re constantly looking at it to ensure we’ve reviewed it and tuned accordingly.”
The tight margins the teams are working to are reflected in McLaren’s practice across the last two seasons of giving Lando Norris an update (or, in the case of Miami, a bigger update) a race ahead of Oscar Piastri.
Having effectively two different car specifications operating at the same time is complicated – even without the obvious human factors to consider – but the thought of voluntarily leaving a couple of tenths back at the factory, waiting until a full suite of parts is available for both cars, doesn’t sit particularly well with the narrow margins of the F1 grid at the moment.
McLaren often follow the practice of putting an update on Norris's car one race ahead of running it on Piastri's
The factory as a performance generator
The modern F1 factory is a formidable tool for generating performance: resources – be they people, material or tools – are fed in at one end; a constant stream of cars and upgrades comes out of the other.
McLaren are celebrating 20 years ensconced within their McLaren Technology Centre – but for other teams, it’s new to have this type of purpose-built mega-factory. Aston Martin opened the first part of their new home last year. They’re set to spread into Building Two shortly after the summer break, with a wind tunnel due to come online in the near future.
“It’s been a game-changer for us,” says Performance Director Tom McCullough. “It’s especially true for design, production and manufacturing, where the people drawing the parts can go downstairs and talk to the people machining, laminating or fabricating the parts, with more and more being done in-house.
“It’s good for communication, good for quality, good for turnaround times, there's less paperwork, less phoning up suppliers. It gives us more control of our own destiny.
“If you’re drawing a part, releasing a drawing, you know the name of the person who’s going to be making it. You can go talk to them, get their advice and input. They can do the same back to you. They can point out how perhaps a minor change will save time. It’s hard to explain how important that communication is until you see it happening.”
Aston Martin are perhaps not having a stellar year – but they have entrenched themselves firmly as a top-five team, supplanting the works Alpine effort, which shows a certain direction of travel. The new factory, argues McCullough, allows them to compete, with a faster, more efficient production process being a crucial part of getting more out onto track faster.
Aston Martin believe that their new factory is crucial in helping them to bring new parts at a faster rate
“This is a development race. Things like having our own wind tunnel, our new simulator, the new factory, it just makes us more efficient. And the cost cap era is an efficiency game. Everything is about efficiency.
“Fundamentally, we have Sporting, Technical and Financial regulations: if you’re more efficient with your time, your resource, you can do a better job, have more money to develop the car, get parts to the car quicker. You’re competing against nine other teams that are doing the same. So, all those little wins that you can grab, from an efficiency perspective, just help you be more competitive.”
This is still a sport for people
McCullough and Thynne both make the point that having good communication between the people designing the part and the people making the part tends to drive the operation – but this is just as important to teams who don’t have a gleaming, purpose-built factory. Jody Egginton is Technical Director for the RB team and agrees that having people talk to one another is the way to pick up efficiency in the operation.
“It’s a really interesting topic. On the one hand, you have a wide range of experts, very focused on their tasks, but on the other, what we buy into as a team is making sure everyone also has an overview and an understanding of what other people’s challenges and concerns are.
“We try to get people talking to each other in the quieter moments, make sure that project management has the drawing office working with production to understand if the manufacturing techniques to use are reliable and robust; that the lead times are sensible, that the scrappage rate is acceptable. And only when we’re comfortable something is going to work in a production environment, will we push it through.”
Egginton professes a degree of satisfaction that RB's updates this year have arrived a race ahead of schedule.
RB Technical Director Jody Egginton has spoken of the importance of communication amongst the team during the production process
“It’s massive. If you have an upgrade worth two-tenths of lap-time, and can bring it one race earlier. That’s fantastic. You have access to a bit more car performance.
“It's a philosophy of the company where we push everybody to try to be as efficient as they can, and flag the things that are stopping them being efficient. We're very, very focused on asking ourselves: can we do that a bit quicker? What prevented that update getting over the line a race earlier? And then dealing with that critical path.
“Human nature can sometimes get in the way. Everyone has a bit of a margin because they don't want to let the team down, but when you add all of those margins together, all of a sudden, you realise it could have been done quicker, so we try to look for the best we can do, and work on that basis – but then, if we do struggle to beat that optimistic timeline, not to start pointing fingers.
“It is a quite a different mentality. Part of the job is making sure people feel comfortable to challenge themselves, safe in the knowledge that, if something unexpected happens, they're not going to be blamed. We don’t do blame – we do: review what went on and try to improve.”
Returning after the summer break, the design offices of the 10 teams will have their attention firmly focused on 2025 – though the many close battles in the field may mean the book isn’t quite closed on 2024. The manufacturing operations, however, will still be living in the moment, with at least one – possibly more – updates on the way in the weeks and months ahead.
We’ve already seen game-changers this year, and the balance of power may shift again before the season is done. We want to see the great moments on track, the spectacular pit stops, or the brave strategy calls deciding a championship – but behind the scenes, an awful lot of hard work and thought in a factory is just as likely to tip the balance.
YOU MIGHT ALSO LIKE
News ‘There was nothing more I could have done’ – Antonelli searches for positives after ‘difficult’ Monaco weekend
News ‘This is just the start’ – Stella backs Norris to hit top form after ‘cold blood’ Monaco victory
News ‘I’m driving at a high level’ – Alonso defends start to 2025 after Monaco power unit issue denies him maiden season points
Feature IT’S RACE WEEK: 5 storylines we’re excited about ahead of the 2025 Spanish Grand Prix
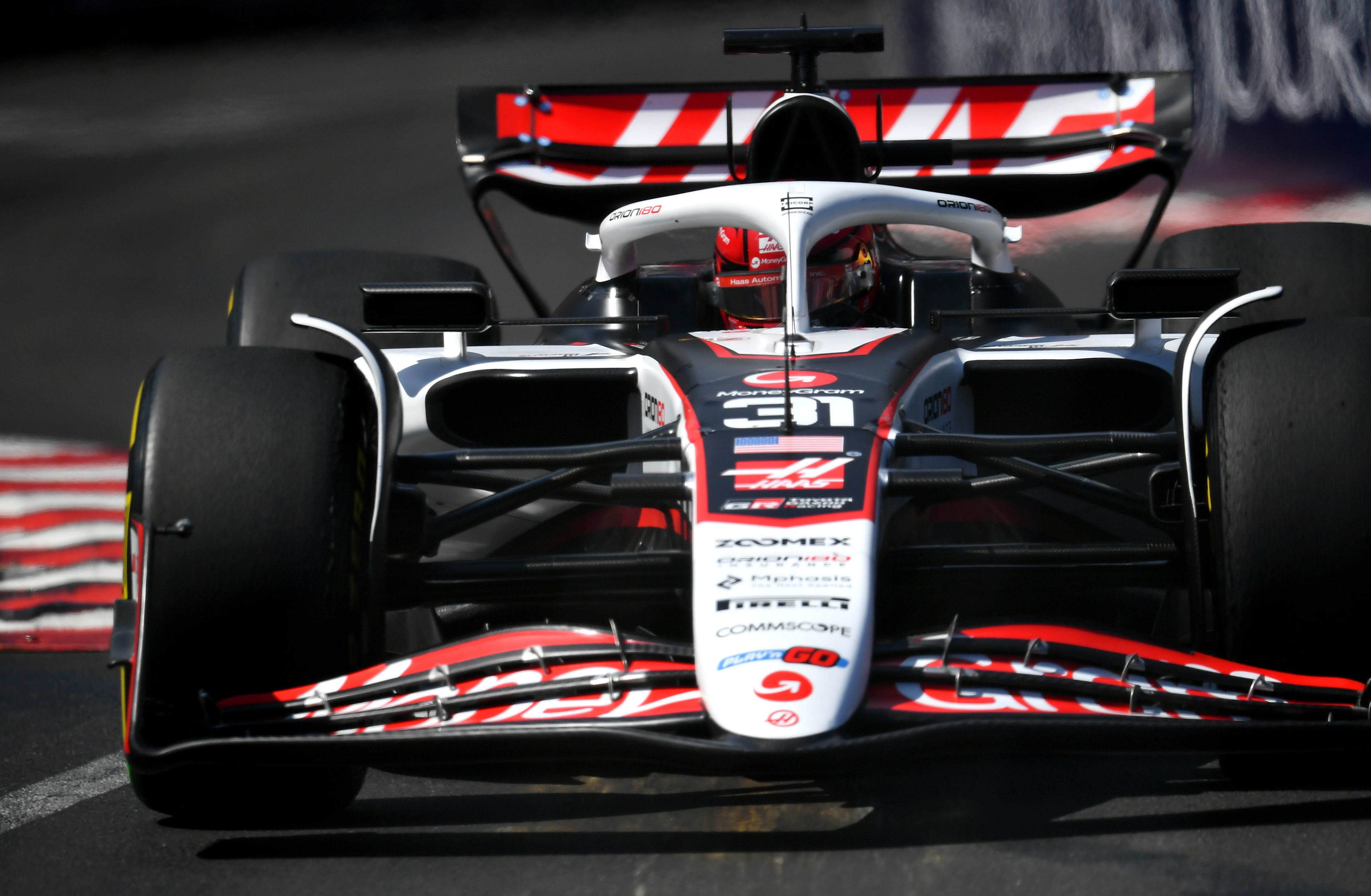